For the flexible packaging industry, VOCs generated during the production process are the most important safety concerns of the company. To ensure safety, the concentration of exhaust gas produced during production cannot exceed 25% of the lower explosion limit (25% LEL).
With the successful launch of ESO, the technology can help flexible packaging gravure companies reduce hidden costs and bring new profit points. Through testing, ESO can reduce printing quality and reduce solvent residue while reducing wind and energy. However, many current flexible packaging gravure companies still have concerns about the safety of ESO enrichment effects.
Below, the author on the gravure equipment after the connection of ESO, how to ensure production safety, detailed analysis and explanation, hope to help the industry to eliminate concerns and achieve VOCs standards discharge.
VOCs emission characteristics and control
In general, the film gravure process includes one white full version and several color ink layouts . In most prints, the total amount of solvent volatilization in the ink screen is less than the amount of two full-color inks, and the total amount of solvent volatilization in the full-color version is generally 30% to 50% of the full version of the white ink.
It can be seen that in the film gravure printing, the solvent of the white ink full version has the largest amount of evaporation , and generally accounts for 50% or more of the total amount of solvent volatilization, that is, the main link of generating high concentration VOCs in the film gravure process is white ink full printing. Therefore, after the ESO is connected to the gravure printing device, the airflow along the inlet and exhaust air mains of the ESO, the white ink full version should be ranked last, as shown in Figure 1. Moreover, according to the difference between the printing and the printing, the airflow direction of the ESO inlet and outlet air mains is set in a targeted manner. In the last color of the white ink in the printing , the airflow in the ESO inlet and exhaust manifold is from the unwinding end to the winding end; the opposite is printed , the white ink is in the first color, and the airflow in the ESO inlet and exhaust manifold is From the winding end to the unwinding end.
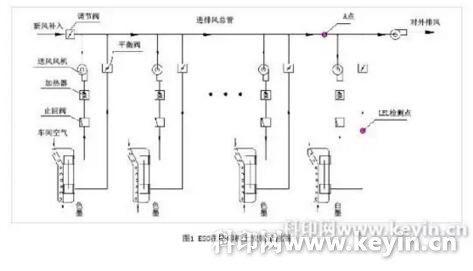
ESO selection
The ESO selection shall be determined according to the printing process parameters of a product with the largest amount of solvent volatilization in the conventional printed matter of the flexible packaging gravure printing enterprise. For example: an 8-color printing machine of a flexible packaging gravure printing company, when producing a certain printed matter, the total amount of solvent volatilization is the largest, about 70kg / h, the solvent component is ethyl acetate, n-propyl ester, etc. (here is convenient for calculation, all press Calculated by ethyl acetate, the lower limit of ethyl acetate explosion is 85.7g/N.m3), wherein the total amount of solvent evaporation of 7 color ink plates is about 30kg/h, and the evaporation amount of a white ink full version is about 40kg/h.
Spin Mop,Spray Mop,Floor Mop,Best Mop
Ningbo Topwill International Trade Co., Ltd. , https://www.nbtopwell.com