[China Packaging Network News] Why do manufacturers need to spray the packaging box?
Internal delivery goals
If the package is used for internal transportation and storage of the company, the code usually contains a simple SKU quantity and packing content. If the shelf life of the loaded items is short, you can also add a production date or expiration date to facilitate the subsequent packing or storage of subsequent products.
Manufacturers promote
Manufacturers usually provide information about the packaging box to help customers and customers' customers identify the contents of the box. They usually identify the logo, graphics, and product name, product number, size, number of parts, and weight on the package.
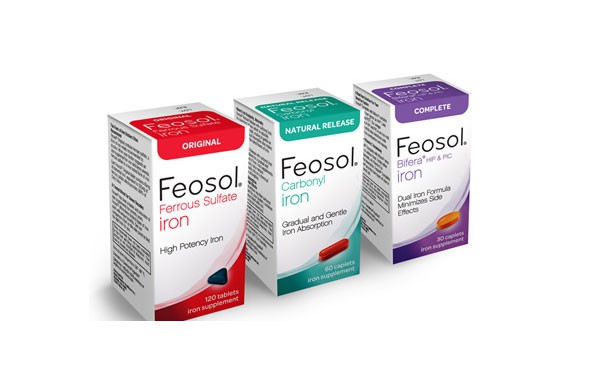
Customer promotion
More and more customers are demanding that specific codes (alphanumeric or bar code) be printed on the product packaging in order to manage inventory during receipt and storage. If the customer has a "machine-readable" receiving system and scans the barcode content into the internal system, the customer will have very specific requirements for the type and content of the barcode.
Guidelines to promote
It is very encouraged to adopt certain industry coding standards in different market segments. Although there are no explicit legal provisions, industry practice can encourage companies to adopt and standardize the packaging code to meet established objectives. For example, the Agricultural Product Traceability Plan (PTI) puts forward specific requirements for the contents, structure, and location of the packaging code to achieve backward traceability of the produce from the consumer table to the origin.
What type of coding is printed on what surface?
People use different types of printers to meet different coding requirements. Selecting a coding scheme requires an understanding of the coding requirements of the package, the coding method, and the material type of the package.
Fixed data
Fixed data is text, barcodes, and graphics that do not change at all stages of the product. In the past, fixed data was often used for products that had a long shelf life or did not require traceability of the source, production date, or batch. However, with most, if not all, sense of responsibility enhancement in the industry, the practice of using only fixed data has been eliminated. As the number of products supplied continues to grow, the number of SKUs in the company's merchandise has also increased. Currently, fixed data on packaging boxes often amplify certain types of variable information.
Variable data
Variable data allows changes in batch, time, and production date, SKUs, production lines, and more. Like fixed data, text and barcodes are the most common variables. However, in order to reduce inventory, many manufacturers treat logos and graphics as variable data and print them online.
Carton Material/Base
The package base is the third factor to consider when choosing a coding solution. The box base is divided into two major categories: porous and non-porous. Porous substrates are usually corrugated boxes. Whether it is kraft paper (brown) or cardboard (white) crates for oyster barrels, it has a multi-aperture and good-absorbent surface. A variety of coding schemes can be used.
Nonporous substrates include shrink bags, clay coated laminated paperboard, and painted finishes. These containers are often used for cost savings, such as shrink bags; or for brand display purposes, such as laminated cardboard and protective coatings. For the latter, the significance of the carton display is greater than its packaging role (shelf-type packaging). The available coding options for non-porous containers are generally limited.
Package Printing Technology Solution
After understanding the coding requirements and the substrate of the package itself, the final step is to understand the possible packaging technology and its advantages and disadvantages. There are two main categories of packaging technology: contact and non-contact.
Contact printing
The coding of the packaging starts with contact printing. This technique is still a viable solution for proper application. In contact printing applications (such as preprinted boxes, labels, and rollers), there is physical contact between the box and the printing device.
label
Among all non-contact printing methods, labeling is the most flexible method. Labels can be printed on the outside of the production line, or they can be printed on-line and then affixed to the packaging box. Although some labels are manually affixed, this method is generally only suitable for small batch applications. Manufacturers are increasingly using a labeling and labeling machine (LPA) system to print labels and attach them to each package.
Advantages: The label can provide high quality, high-resolution print quality. The labeling system can print code that is always clear and easy to read. These codes can be read manually (manually) or mechanically (such as scanners, cameras, or verifiers). Since the encoding is created digitally, the tag is also the only contact printing method that can provide a variable data solution.
Disadvantages: Labels are the most costly type of printing solution, and sometimes even more expensive than all other alternatives. Labels also require more intervention than other contact or non-contact methods because of their higher frequency of replacement, which in turn affects the uptime of the production. Most label printing systems also require the use of ribbons, where the ink in the ribbon is transferred to the label. Labels and ribbons must be replaced on a regular basis, and the frequency of replacement depends on the amount of production. It is possible to change them many times a day, and to interrupt production when replacing labels and ribbons. In addition, labels and ribbons are often replaced before they are completely used up, which increases the number of labels and ribbons that are wasted, leading to increased label costs.
Preprinted packing box
One of the earliest and most widely used solutions in the packaging code printing is preprinted packaging. This program provides excellent print quality for fixed data. Preprinted packages are almost always printed by the container supplier.
Advantages: Pre-printed containers offer consistently high levels of print quality. This process supports a higher resolution, enabling the box material to handle and allow the use of color graphics composed of multiple colors.
Disadvantages: Preprinting applies only to fixed data. When managing multiple projects, the user needs to use a separate box for each SKU, which consumes a lot of storage space. Changing the product configuration, adding content, etc. requires a longer lead time, and due to outdated data, waste can occur.
Rolling machine
Rollers are online printing methods. As the name suggests, the operation principle of the roller printer is that the roller first rolls over the ink-containing area, and then the rubber pad is pressed on the packaging box so that the code is printed.
Advantages: The squeegee is a low-cost way of marking the box and is usually used for operations with a lower yield/SKU.
Disadvantages: The squeegee needs to use a separate rubber pad for different codes, which increases inventory and increases the management of the rubber pad, thereby increasing costs. If the spare rubber pad is not in storage and the existing rubber pad is damaged, you must go to another job to produce, or wait for a new rubber pad, and this process may take several days. The same applies to situations where new SKUs need to be added without planning ahead. The use and management of ink is often very messy and can affect the quality of the code. Switching between different encodings creates further challenges and may cause confusion. In addition to replacing the wheel, this method is only suitable for fixed data encoding.
Non-contact printing
Due to the increase in packaging code requirements and the company's lower cost requirements and higher flexibility in the printing methods of containers, non-contact printing options have begun to emerge and have been developed with different on-demand printing technologies. .
[pagebreak]
Piezo - High resolution
Piezoelectric inkjet technology generally refers to "high resolution" large character printing. This technique is often used on production lines to print quality barcodes, logos, text, and other prints on the packaging. Advances in piezoelectric nozzle technology have significantly improved the quality of graphics. Sometimes people mistake the piezoelectric printing code for pre-printing.
Advantages: Piezoelectric technology can provide high-quality, high-resolution print quality, and is suitable for a variety of applications such as bar code printing, text, graphics, and logos. This technology is a lower-cost solution compared to contact-type variable printing solutions. If properly maintained, piezoelectric based systems can print high quality, manual or machine readable codes. Because the encoding is created digitally, jobs can be changed quickly to meet different SKU requirements, and new jobs can be added in minutes. Ink supply is usually sufficient to meet the needs of most companies for multiple shifts and even days. Systems equipped with an automatic cleaning function can be run during production shifts and minimize intervention (if any). This system usually only requires short maintenance during shift changes.
Disadvantages: Piezoelectric high resolution technology is generally only applicable to porous surfaces, which limits the type of substrate that can be applied. In order to obtain the best print quality, the print head needs to be close to the print surface, and in some cases it will almost touch the surface. This can cause problems if the location of the package is not exactly the same at each print.
Thermal Inkjet (TIJ)
Thermal inkjet, also known as TIJ, is a relatively new package printing solution. Using the same thermal spray technology as the office and home desktop printers, this series of printers is easy to use and has a higher resolution than valve or piezo inkjets. In general, it is a cartridge-based solution that integrates the printhead into the cartridge.
Advantages: TIJ is easy to use and maintain. Without having to master high skills, you can maintain the TIJ system and change the ink. After each ink cartridge replacement, the system will use a new nozzle to restart. This ensures print quality and easy recovery.
Disadvantages: The nozzle print height is usually 1â„2 inch (13 mm). Therefore, in order to print a bar code and many graphics or logos, the nozzles need to be spliced ​​together, and often show gaps or overlapping lines on their prints. Each time you replace the ink cartridge to maintain alignment, you must recalibrate the stitching. Similar to piezo inkjets, the TIJ-based system nozzles need to be close to the print surface for almost the best print quality, and in some cases almost touch the surface. The combination of ink and nozzle cartridges increases operating costs. Regardless of the state of the nozzle itself, the user must replace the nozzle when changing the ink. If the printhead is damaged and must be replaced, you must also discard any remaining ink.
Valve Inkjet
Valve inkjet is the first non-contact packaging technology. The ink flows through the pressurization system. In this system, the ink droplets are formed by the closing of the valve, and the ink droplets penetrate into the surface of the package under the pressure.
Advantages: Valve jets can print fixed data and variable data at a lower coding cost. This technique is suitable for porous surfaces and non-porous surfaces.
Disadvantages: Valve inkjet is only suitable for printing text and low resolution graphics. Without proper maintenance, the system is often messy.
Choose package printing program 3-step method
1 Flexibility
Choosing the package coding system can be difficult, depending on your need for coding and the surface of the package. In general, users find it more advantageous to adopt more flexible solutions that support current and future applications.
2 Maintenance
The market for non-contact coding solutions continues to grow, driven by the growing demand to reduce costs and inventory. Cleaning and maintaining the coding system is critical to its success. Let's consider the way and frequency of performing maintenance.
3 Quality and cost
Text-only solutions may take longer to run, sometimes providing unsatisfactory results that are still legible.
High-resolution systems (including labels, piezo and TIJ) require periodic intervention to maintain consistent print quality. This is very important because the quality of the dropped barcode prints can lead to unreadable data and may also cause the product to be returned. At present, some piezoelectric-based systems provide an automatic cleaning function, which helps maintain the encoding quality. Below, we consider the print quality and work efficiency. Is the frequency of automatic cleaning sufficient to ensure the best print quality? Does cleaning disrupt production? Is it possible to perform cleaning during normal operation without affecting production? How to deal with the cleared ink? What is the cost of the removed ink? Maintaining print quality is critical, but what costs will it generate?
Hydra Facial Machine,Hydra Beauty Machine,Hydra Facial Machines,Professional Hydrafacial Machine
Guangzhou Lesen Xinpin Electronics Co.,Ltd , https://www.lesenxinpin.com