In the cap packaging industry, wine bottle cap packaging is a huge branch, which is more profitable and demanding than other types of caps. At present, the bottle cap materials on the market mainly include plastic, glass, metal, aluminum and plastic. Among them, the cost of plastic bottle caps is lower than other types, and the application is more common. Most of the materials are ABS plastic or PP plastic, and the traditional printing process is screen printing. The correct control of the production process in high-volume, rapid production processes is an important prerequisite for ensuring the quality of plastic bottle caps and reducing waste or defective products. This requires operators to screen-making, screen printing production processes, and nets. In-depth understanding of printing quality problem analysis. In this regard, the author summarizes some practical experience and shares it with industry professionals.
Web page production points
Firstly, the mesh is stretched with a mesh of 250 to 300 mesh. Since the mesh cloth is made of nylon mesh cloth, a mesh mesh of 300 mesh is generally used. If the thickness of the ink layer needs to be increased in a special pattern, the mesh is selected. cloth. After the stretched mesh glue is completely dried, a layer of photosensitive adhesive of a certain thickness is uniformly coated on the surface of the mesh cloth, and then the photosensitive adhesive is sufficiently dried by air drying or other drying methods. Then put the film and frame on the exposure table, adjust the position of the printing plate, cover the blackout cloth, and turn on the exposure lamp for exposure. Finally, the exposed screen is immersed in clean water for 1 to 2 minutes, and the plate is developed with tap water.
Plastic wine bottle cap screen printing production process and process control points
1. Screen printing production process
The heating oven was turned on for preheating, and the heating temperature was set to 40 to 50 °C. Seal the four non-patterned areas of the frame with tape, then install the machine, adjust the position and turn on the power. Open the vacuum pump and place the plastic bottle cap to be printed on the fixed mold, and accurately position it by adjusting the position of the frame. First test printing, after the quality is qualified, adjust the automatic capping equipment and the automatic capping equipment. When the heating oven reaches the predetermined temperature, it can be mass-produced.
2. Process control points
The screen printing production requirements of plastic bottle caps are different from those of aluminum plates and papers. Because plastic parts are easily deformed after being heated, the bottle caps are more stringent in size, so the oven temperature of plastic bottle caps must be lower than that of plastics. The deformation temperature of the part itself is generally set to 40 to 55 °C.
In addition, ink type, mesh, printing speed, etc. have certain specialities. Most of the inks use single-component fast-drying inks, commonly used semi-matte fast-drying inks, and quick-drying or slow-drying thinners are added to adjust the drying speed of the inks to adapt to the changes in the temperature of the production environment in winter and summer, sometimes using fast and slow dry dilution. The agent adjusts the amount of ink to be inked to meet the requirements of different production speeds.
Plastic wine bottle cap printing quality requirements
1. The clarity of the pattern
It requires uniform ink, consistent color, clear pattern, no bottom leakage, no joint offset, no indentation and so on.
The thickness and uniformity of the ink layer can be changed by adjusting the mesh number, the number of times of screen squeegee, the viscosity of the ink, and the speed of the squeegee. In addition, the ink should be thoroughly mixed before production to ensure uniform color and viscosity.
Adjust by adjusting the length and width of the film
The joint and width of the whole pattern, the pattern joint is generally controlled within 1mm, the author suggests to choose the blank pattern as the joint as much as possible, which can achieve the effect that the joint is not obvious.
Before using the screen, you must use transparent tape to shield the blank part of the pattern to avoid contamination caused by ink dripping.
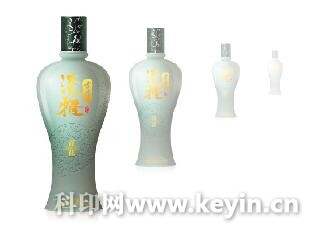
2. Screen printing pattern size and height
The size and height of the plastic bottle cap should be consistent with the standard sample cover, and there is no obvious difference by visual inspection. The deviation of the pattern size should be controlled within ±0.2mm, and the height deviation of the plastic bottle cap pattern should be controlled within ±0.1mm. It can be measured directly using a vernier caliper.
The size of the pattern is adjusted by adjusting the size of the film, and the blade pressure and ink viscosity have little effect on the pattern size.
3. Ink adhesion
The requirement for ink adhesion is: after the plastic bottle cap ink is completely dry, use a special tool to cut it, then use 3M paper tape to paste, use rubber roller to roll back and forth 3 times, tear open 3M paper tape, not Allows a large area of ​​the skin to peel off and delamination, allowing a small area to fall off slightly.
In actual production, the author found that the adhesion of the ink can be adjusted by adjusting the type of ink and the hardness of the coating of the plastic bottle cap coating material. For plastic bottle caps with special quality requirements such as alcohol-resistant soaking or high-temperature sterilization, different varnishes can be selected according to requirements. If it is directly sprayed on the printed plastic bottle cap, then the plastic bottle cap is immersed in 50% alcohol for half an hour, and dried for 3 minutes to test the ink adhesion.
Plastic screen cap common screen printing quality problems and solutions
Color difference
Phenomenon: There is a difference between the batches of plastic bottle cap print patterns or between the standard sample covers.
Analysis of the reason: Since the printed pattern of the plastic bottle cap is generally small in size and the lines are relatively thin, it is impossible to use the color difference meter for colorimetric measurement, and only visual comparison can be performed under a specific light source. The light source generally selects the standard light source box D65 light source, or it can be brighter, scattered natural light, to avoid color contrast under direct sunlight or dark, under-light fluorescent light.
Solution: Try not to use self-adjusting composite color. This is because of the differences in manual ink-adjusting technology and ink types, which makes it difficult to adjust the color to uniformity in each batch production. In this regard, the standard sample cover ink can be purchased from the ink manufacturer, and the amount of ink required for the production of several batch orders can be ordered according to the size of the production batch of the plastic bottle cap, so as to ensure the plastic bottle cap between the batches. The consistency of the color of the printed pattern.
It is worth noting that the mesh number of each pattern should not be easily changed. Once the number of meshes is changed, it is equivalent to changing the amount of ink, which will cause the difference in the thickness of the screen printing ink layer, and thus the chromatic aberration. If the speed and oven temperature are changed during the printing process, the staff should remember to correct and confirm the pattern color again. In addition, from the beginning of new product proofing, the standard sample cover is determined as “deep, medium and shallow†according to the color, and a standard of fluctuation range and color fluctuation range is established to avoid large differences due to different standards in color difference determination. .
2. The pattern appears to be missing a small part
Phenomenon: The printed pattern of the plastic bottle cap is compared with the standard sample cover, and sometimes there is a small part missing in the stroke or detail.
Analysis of the cause: In the process of screen printing of plastic bottle caps, sometimes the ink particles block the mesh of the mesh, which causes the amount of ink in some places to be less or missing. If the missing pattern of the plastic bottle cap printing pattern does not affect the normal recognition compared with the standard sample cover, and the area is less than (2 × 2) mm2, and no more than two places, it is regarded as a good product.
Solution: In the production process of plastic bottle caps, when there are shifts, rests, etc. for a long time, the staff must clean out the residual ink in the screen and wash the screen with special detergent. Avoid blocking the mesh due to ink solidification during shutdown.
The small stroke pattern should be adjusted as much as possible during plate making, that is, the small stroke pattern dots should be merged or removed to avoid ink clogging due to a small stroke with a small number of meshes; on the same screen, more patterns are created. When the screen mesh is clogged, other spare patterns can be replaced to continue production.
Development trend of automatic high-speed screen printing production of plastic wine bottle caps
In recent years, in order to meet the high efficiency, high quality, low cost and other requirements put forward by customers, the automatic high-speed screen printing process of multi-color overprinting has gradually entered the market. This process has also raised high demands on screen printing equipment, ink and mesh. Requirements.
At present, the production speed of plastic bottle caps has been increased from manual to semi-automatic 20 to 30/min to 40 to 70/min. The increase of production speed puts forward new requirements on the chain length, drying time and ink amount of ink in the screen printing equipment oven. In addition, by appropriately reducing the mesh number and increasing the amount of ink, the thickness of the screen printing ink layer can be increased, so that the problem of insufficient ink amount due to excessively high speed during high-speed production can be solved.
In order to reduce the cost and reduce the quality problems such as poor ink adhesion and peeling, inks with low viscosity and high hiding power can be used in the future.
In recent years, UV screen printing inks have been gradually applied in the printing production of plastic wine bottle caps. Under the irradiation of UV lamps, UV screen printing inks can be quickly cured, and the ink layer has high hardness after curing, and the production speed is fast. The advantages of secondary baking, etc., when used on products sensitive to high temperature, the advantages of UV screen printing ink are more obvious, and also lay a foundation for multi-color overprinting on a screen printing device, which can increase the decorative pattern. Increase product added value.
The above content is selected from Keyin Media. Printing Technology ·Packaging and Decoration 》No.7, 2016, please pay attention to the journal channel for more journal content .
Pet Supplies for Christmas
Christmas pets
Shaoxing City Heou Leisure Goods Co., Ltd. , https://www.heoupettoy.cn