[China Packaging Network] In the process of water offset printing, controlling the ink-water balance is more important, and it is closely related to whether the prints are normally transferred, the depth of the ink, the accuracy of color registration, the degree of dryness of the paper, and whether it is dirty or dirty. The key to ensuring product quality is stable.
There are many factors that affect the quality of water offset products, and it is difficult to control them in actual production. Based on accumulated work experience, the author summarized some quality control points and shared them with readers.
Paper inspection
In the printing process, the results of various factors will be reflected on the paper, so the inspection of the paper is very important and necessary. The inspection of the paper in the print job can generally be divided into two stages: start printing and normal printing.
1. Start the inspection of the printing stage
â— Check the color of paper
At the beginning of the printing, the operator should frequently pull the paper, and start a full inspection from both sides of the paper to the sides and in the direction of dragging. Because of paper quality problems, such as the depth of ink, dirty oil, etc., always start from the mouth and gradually extended to the drag. Therefore, when checking, the line of sight should be scanned to see if the entire screen has quality problems and whether the ink is in compliance with the proofs. When the ink of the entire screen or the local area does not conform to the proofs, it should be adjusted in time. The means of adjustment cannot be limited to the adjustment of the ink quantity, and the control of the amount of water should also be considered.
â— Inspection of paper size
After checking the paper color, you should quickly check whether the paper T-line meets the requirements. In particular, the positive and negative printed paper should be checked whether the front and back faces are the same size.
â— Inspection of blots
Dots are the most basic unit that constitutes the color of prints. If the dots are significantly deformed and expanded, they will directly affect the color reproduction and copying effects. Therefore, it is possible to compare the dot-line differences between printed products and proofs by means of a magnifier to observe whether the imprinted dot lines are empty, whether there are significant enlargements and lateral and vertical deformation, ghosting and other quality problems.
In addition to the inspection of paper ink, specifications, and prints, various quality defects that are prone to be produced in the company's production are the focus of inspections at the beginning of the printing stage.
2. Inspection of the normal printing stage
â— Inspection of paper overprint and ink
In the printing stage, as the ink is gradually in balance, the focus of the operator's inspection is still paper overprinting and ink color. It is generally possible to compare the two sides of the paper with the middle part and compare it with the paper that was drawn from the previous several times. In addition, it should also pay attention to whether there is any change in the layout moisture. As for the inspection of the rules, from time to time, 2 to 30 sheets of paper can be drawn, and they can be spread out after the collision. Observe whether the rules are consistent and whether the positioning of the front gauge and the side gauge is accurate.
â— Note the effects of silty, paper, etc.
After a period of continuous printing, dirt such as paper dust, paper hair, and fine ink on the ink easily adheres to the printing plate or blanket, resulting in rough lines or rough hair. In this case, wipe off the ink on the surface. In order to prevent downtime caused by ink changes, it is generally necessary to put 8 to 10 overprinted paper and continue printing. If too much dust adheres and affects quality, plates and blankets should be cleaned.
Water, ink control
In the production process of water offset printing, it is very important to control the ink-water balance. It is closely related to whether the prints are normally transferred, the depth of the ink, the accuracy of color registration, the degree of drying of the paper, and whether the paper is sticky or dirty. It is to ensure the stability of product quality. One of the keys. In the printing process, the depth of printing ink is directly related to the amount of water supply and the layout moisture. However, in production practice, we can not simply rely on reducing the amount of water supply to improve the ink, because the water is too small, lose the balance of water and ink, easy to make the blank part sticky. Therefore, in the printing process, it is necessary to consider whether or not the amount of water supply is appropriate at the same time when adjusting the amount of ink supplied, and it is timely and correctly judged whether the ink is balanced or not. Experienced operators, often on the premise of guaranteeing that the printing plate is not sticky, control the water supply in the smallest possible range, and make the amount of water supply and the amount of ink in a relatively stable state. This will ensure that the paper is consistent in depth before and after ink, and the print job is stable.
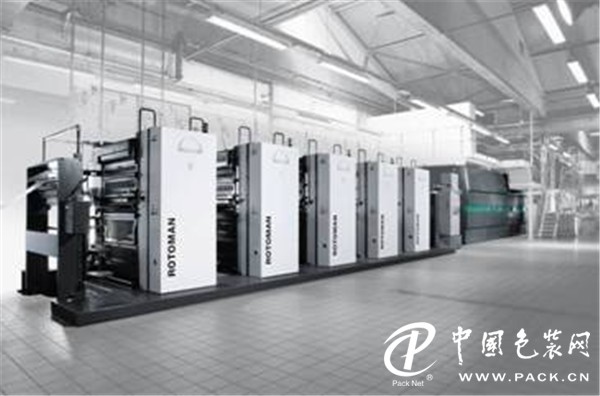
1. Control of water supply
To properly control the amount of water supply, to achieve ink-water balance in the printing process, the correct identification of the layout of water is a prerequisite. For the identification of the size of the water in the layout, so far there is no fixed value, so it cannot be specified as a machine. In production practice, the size of moisture is often identified by the operator visually measuring the strength of the reflected light in the layout. This visual inspection method can play a role in identifying the size of the layout of the water, because a certain thickness of the water film can fill the plate sand, reduce the diffuse reflection and increase the amount of reflected light. However, this method also has certain limitations because of the limitations of various reasons, such as the ratio of the area of ​​the layout graphic and the blank area, the different printing plate materials, the different intensity of the light, and the different viewing angles. The water film does not allow the plate to have the same amount of reflected light. Therefore, in daily printing operations, in addition to the above-mentioned visual inspection methods, it is also possible to observe from the following points. If the following conditions occur, it indicates that the layout surface is excessively moist. 1 Use a knife to scoop the ink on the ink roller, leaving a small drop of water on the ink knife; 2 There are small drops of water on the transfer roller, and there are also drops of water in the ink tank; 3 The layout often appears to be dirty or after a long shutdown. Still no sign of dryness; 4 imprinting emptiness, sulking of mouth wavy and pale, dull and dull ink; 5 paper curling soft and weak, uneven; 6 rubber roller dragging slightly small water drops; There is a big gap between the paper at the time of printing and the paper color before the machine stops.
[pagebreak]
2. Master the relationship between ink and ink
In the printing preparation process, when the work of loading plates, loading paper, and adding ink to ink fountains is completed, the ink color correction and color correction are required. When adjusting the moisture content, consideration should be given to the size and distribution of the layout, the thickness of the imprinted ink layer, the properties of the printing paper, the properties of the ink, the type of the printing plate, the speed of the machine, and the ambient temperature of the shop. When coloring, if you feel that the ink is lighter, you can adjust the amount of ink, of course, but you can't ignore the effect of moisture. Both ink and ink should be considered at the same time. In general, for PS plates, smooth paper, the moisture content may be slightly smaller; for rough paper, the moisture may be slightly larger. When the machine is running at high speed, the moisture content can be slightly smaller; for low speed machines, the moisture can be slightly larger. In addition, environmental conditions and temperature and humidity can not be ignored. Since the layout water is distributed in both direct and indirect forms, most of the moisture will be emitted into the air, in addition to meeting the printing ink balance requirements. Therefore, the higher the ambient temperature, the quicker it will be. Sometimes encounter the oily ink Add the gum in the fountain solution, the paper is rough, fibrous tissue loose and easy to lint and powder, the amount of additives in the ink after the improper use, etc., the original ink relationship will change.
The fluidity of the ink is also affected by the temperature. When the temperature is low, ink fluidity is relatively poor. When the temperature of the machine rises, the fluidity of the ink becomes better. Therefore, the same ink fountain screw adjustment amount, the amount of ink ink will also be different. In order to maintain the consistency of the ink before and after the paper as much as possible, attention should be paid to changes in the amount of ink under the ink. During the printing process, new inks can be gradually replenished, keeping the ink flow as relatively stable as possible.
For the ink-and-wash balance, we cannot simply look at the amount of use of the two. Since the water used for offset printing is not pure water, it contains a certain amount of an aqueous solution of an electrolyte and a hydrophilic colloid, constituting a hydrophilic colloid system. The ink is not completely non-polar oil, in addition to the connection material, but also contains pigments, spices and other substances to form a water-repellent colloidal system. Therefore, the relationship between ink and water is not only the relationship between water and oil, but also the relationship between hydrophilic colloids and water repellent colloids. Water and ink are essentially not mixed at rest, but under the influence of emulsifiers and ambient temperature conditions and pressure, the two will mix to some extent. This emulsification is more or less penetrating the entire printing process. The key is that the amount of emulsification should be controlled within a certain range.
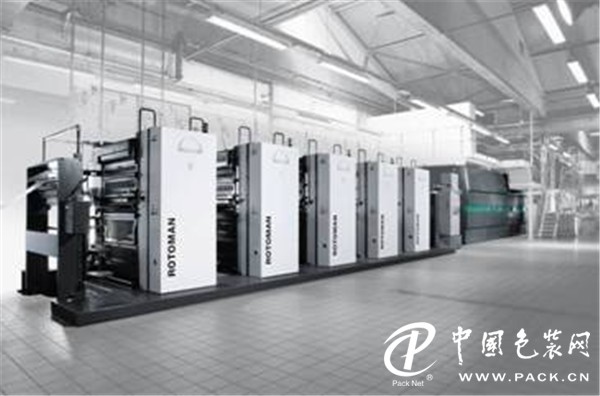
3. Control the pH of fountain solution
During the printing process, not only the amount of fountain solution but also the pH of the fountain solution should be taken into consideration. The PH value should be maintained at 5 to 6, because the PH value is too low or too high can cause some bad results.
If the PH value is too low, problems such as corrosion of the printing plate, deinking of the ink roller, drying of the imprint, and the like may be caused. This is because the plate of the PS plate is aluminum, and the hydrophilic part is the alumina layer. The aluminum oxide layer will not be corroded under weak acidic conditions, but it will be eroded under strong acidic conditions. That is, the blank part of the sand is eroded away. If the corrosion is further aggravated, the metal plate base of the graphic part will be damaged, causing lines and dots on the plate to fall off. The strongly acidic dampening solution reacts with the surface of the metallic ink roller to form a hydrophilic salt layer on the surface thereof, thereby forming ink roller deinking and affecting the normal ink transfer. If the dampening solution is too acidic, the desiccant in the ink will be changed and the drying effect will be lost. As a result, the ink will not easily dry and the imprinting will be easily dirty.
If the PH value is too high, it will cause problems such as dirty prints, graphic off, and ink emulsification. This is because the hydrophilic layer of the blank portion of the printing plate may be damaged by friction during the printing process, which requires the acidic solution to react with the plate base metal in time to form a hydrophilic salt layer to supplement the damaged portion. If the pH of the fountain solution is too high, the process of repairing the damage will not occur or occur slowly, resulting in a dirty appearance. The graphic part of the PS version is a hardened photosensitive resin that dissolves in an alkaline solution, causing images to fall off. The high pH value of the fountain solution will also make the ink free fatty acid ions. It is an anionic surfactant, which can reduce the surface tension of the fountain solution and the ink and cause the emulsification of the ink to increase.
C&S PAPER CO ., LTD , https://www.cstissue.com